Монтаж
Виконуємо монтажні роботи на всій території України та за її межами.
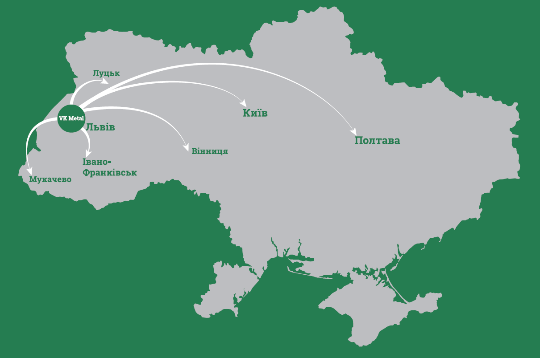
Лазерна порізка металу дозволяє отримати фігурний візерунок і рівний край зрізу без окалини.
У порівнянні з плазмовою, лазерна порізка металу є дешевшою. Такий метод порізки металу дає можливість втілити в життя будь-яке різьблення та дизайн задовільнивши найвибагливішого клієнта. Адже, за допомогою чітких креслень та лазера можна отримати максимальну точність деталі.
Лазерна порізка металу є практично безвідходним виробництвом. Процес лазерної порізки зазвичай замовляють у комплексі з іншими видами обробки листового металу, такими як гнуття металу, зварювання і порошкове фарбування. В результаті цього готова продукція буде мати ідеальну точність кутів і розмірів.
Лазер дає можливість домогтися отримання самих маленьких отворів і розрізів. Варто зазначити, що лазер є найбільш безпечний для металу, який має дзеркальну або глянцеву поверхню, оскільки на ній він не залишає пошкоджень.
Ми втілюємо будь-які дизайнерські рішення, що стосуються оформлення металевих виробів і конструкцій з елементами лазерного різання. Важлива перевага даного методу різки металу порівняно з іншими полягає у низькій ціні, швидкому виконанню замовлення та високій точності.
Сутність термальної обробки полягає у зміні структури металів і сплавів у зміні їх механічних та фізичних властивостей. Існує три стадії термічної обробки:
1. Нагрівання до необхідної температури;
2. Витримка при цій температурі (1 хвилина на 1мм перерізу деталі);
3. Охолодження.
Усі метали та сплави складаються із кристалічних зерен. При нагріванні до необхідної температури більшість кристаликів руйнується. Під час різкого охолодження на місці зруйнованого кристалика зароджуються багато маленьких кристаликів та утворюється дрібнозерниста структура. Чим менший кристалик, тим міцніше вони пов'язані між собою, як наслідок - велика твердість. Проте, утворюються внутрішні напруги, які надають загартованій деталі крихкості. При наступному нагріванні до невеликих температур кристалики починають плавитися. Цей процес призводить до внутрішньої напруги в кристаликах і, відповідно, зменшується крихкість. При подальшому нагріванні кристалики руйнуються.
Наші спеціалісти є добре обізнані та мають практичний досвід у термічній обробці металу. Ми виконуємо, як невеликі разові замовлення, так комплексні проекти пов’язані з обробкою металу.